- Material Related
- Design Related
- Handling Related
- Failure Mode: Etching
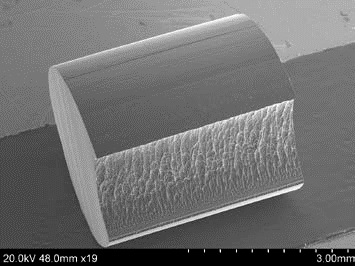
-
Description
As the O-Ring is etched by the process environment (radical, ion), the extent of etching can be confirmed either using a microscope, profile projection, or SEM.
-
Resulting Effect
Excessive etching can result in particle contamination, leaks.
-
Countermeasure
- Use a material with improved plasma resistance
- Move seal location further from the process environment
- Failure Mode: Adhesion
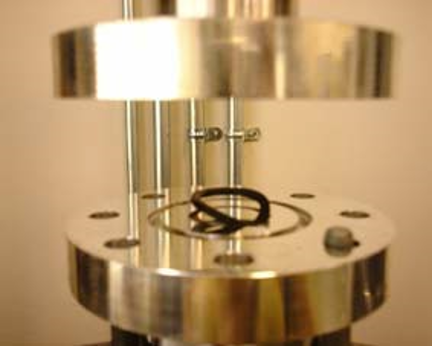
-
Description
A combination of thermal and chemical effects that causes the O-Ring to adhere to the groove or opposing face. Adhesion can be caused by a combination of bleeding, physical conformation to the opposing surface, and intermolecular forces.
-
Resulting Effect
Residue upon O-Ring removal, contamination.
-
Countermeasure
- Apply a slight amount of grease
- Adjust surface roughness (O-Ring, counterface) while retaining seal performance
- Lower operating temperature, raise release temperature
- Failure Mode: Cracking
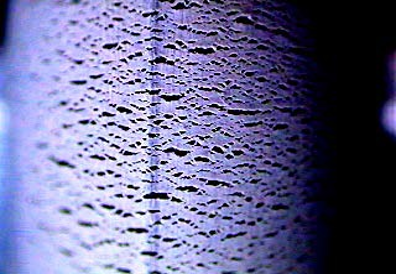
-
Description
Surface defects caused by a combination of attack (thermal, plasma, physical, UV) under elongation, stress concentration. Small surface cracks are often caused by material degradation, and larger cracks from stress concentration.
-
Resulting Effect
Particles, Leaks, Accelerated Etch Rate (decreased PM cycle)
-
Countermeasure
- Limit elongation amount to 1~3% for static face seals.
- Optimize groove to avoid stress concentration
- Practice proper storage (avoid excess heat, UV exposure)
- Failure Mode: Ozone Degradation
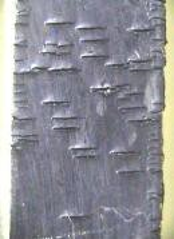
-
Description
Ozone attacks polymers chains to cause cracks perpendicular to the strain axis.
-
Resulting Effect
Cracks and fractures may cause leaking.
-
Countermeasure
- Avoid humidity and stress when storing.
- Select an Ozone resistant material.
- Failure Mode: Blistering / RGD
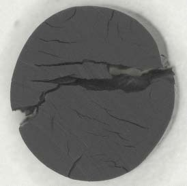
-
Description
Rapid Gas Decompression (RGD) occurs when the polymer matrix is unable to withstand the release of entrapped gases during a sudden drop in pressure.
-
Resulting Effect
Cracks and fractures may cause leaking.
-
Countermeasure
- Selection of a material with low gas compatibility and high pressure resistance.
- Failure Mode: Swelling
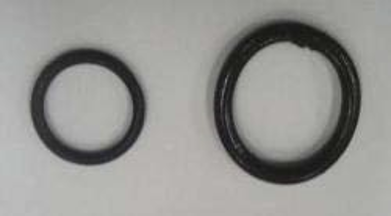
-
Description
Swelling occurs when solvents are able to enter the polymer matrix due to affinity.
-
Resulting Effect
O-Ring protrusion from the groove can lead to fracture and leak.
-
Countermeasure
- Selection of a material with low compatibility to the select medium
- Failure Mode: Permanent Deformation
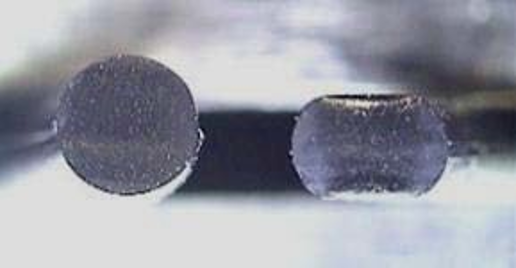
-
Description
Permanent deformation occurs when thermal stress breaks cure points in the polymer matrix. As a result, the O-Ring’s ability to elastically recover from deformation is reduced. Compression Set is a measure of this permanent deformation.
-
Resulting Effect
Leak, Clearance Compromise
-
Countermeasure
- Reduce seal location temperature
- Selection of a material with higher temperature resistance
- Failure Mode: Hardening / Softening
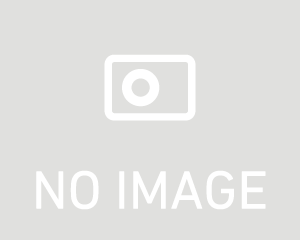
-
Description
Similar to deformation, hardening/softening occurs as the polymer’s elasticity (compression set) is compromised. Whether the polymer hardens or softens depends on mechanism of the polymer chain degradation.
-
Resulting Effect
Hardening: O-Ring cracking and fracture can lead to leaking Softening: Adhesion and contamination to the groove and counterface. Leak from increased deformation.
-
Countermeasure
- Selection of appropriate material
- Failure Mode: Bleeding / Contraction
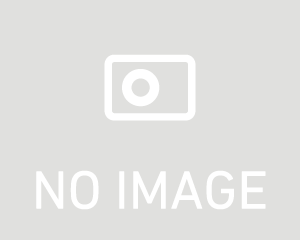
-
Description
Low molecular weight oils seep out from within the polymer towards the O-Ring surface under dry conditions.
-
Resulting Effect
Excess bleeding can result in dimensional contraction of the O-Ring.
-
Countermeasure
- Reduce internal stress in deformed state
- Selection of appropriate material
- Failure Mode: Groove Detachment
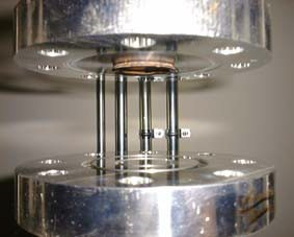
-
Description
Adhesion, Twisting, Dimensional Incompatibility leading to the O-Ring detaching from the groove.
-
Resulting Effect
Increased internal stress leading to material failure and leaking.
-
Countermeasure
- Material selection combined with proper installation practices
- Twisting is considered as one of the main causes of detachment
- Lowering operation temperature, raising temperature during release
- Failure Mode: Abrasion
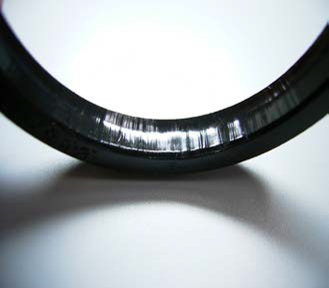
-
Description
Observed in seals for locations with rotating and reciprocating motions. Coefficient of Friction increase caused by: Grease depletion.
-
Resulting Effect
Contamination, temperature increase, surface roughness increase
-
Countermeasure
- Eliminate the causes above or consider a custom design/material such as a resin
- Implement a design specialized for the dynamic application
- Failure Mode: Protrusion / Biting
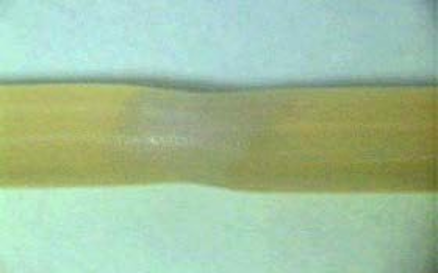
-
Description
Twisted installation, groove overfill, CTE considerations, over pressurization.
-
Resulting Effect
Biting leads to deformation, discoloration, and jamming
-
Countermeasure
- Custom design that provides a cavity for squeeze
- Failure Mode: Crushing
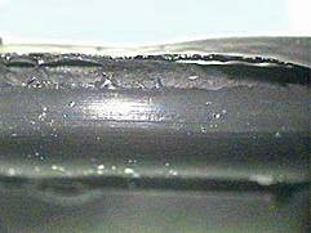
-
Description
High temperature over-compression causes crushing for materials with insufficient mechanical strength.
-
Resulting Effect
Material failure caused leak
-
Countermeasure
- Reduce temperature
- Design for appropriate groove fill at the application temperature
- Implement seal design to reduce internall stress
- Failure Mode: Twisting
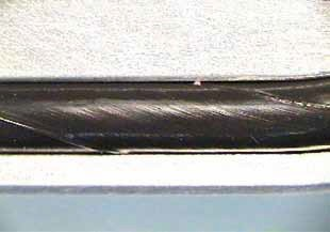
-
Description
Permanent twisting occurs when 1) the opposing face’s motion is not purely in the z-direction, and 2) the O-Ring cannot recover from the imposed twist.
-
Resulting Effect
If the parting line crosses the seal surface, it can lead to a leak.
-
Countermeasure
- Implement seal design resistant to rolling
- Failure Mode: Scratching
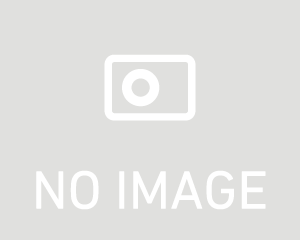
-
Description
Scratching often occurs during removal and can cause weak points where stress can concentrate.
-
Resulting Effect
Material failure caused leak
-
Countermeasure
- Pull the O-Ring perpendicularly out of the groove at all points. Pulling at an angle can cause the O-Ring to catch the groove edge and scratch, especially at entry-points.
- Implementation of custom design for easier installation and removal